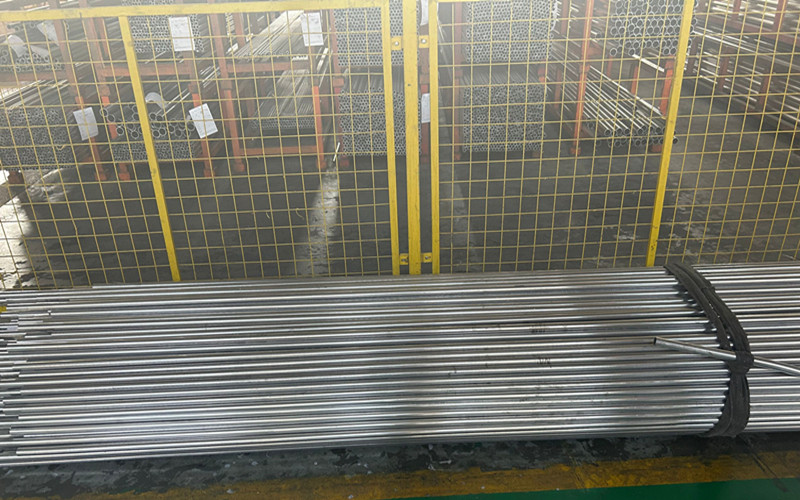
4343/3003/4343 Aluminum High-Frequency Induction Welding Tube 4343/3003
- Description
The 4343/3003 and 4343/3003/4343 aluminum high-frequency induction welding tubes are essential components in heat exchangers, radiators, and cooling systems, each offering distinct structural advantages and performance characteristics. The 4343/3003/4343 tube features a three-layer composite structure, where the inner 3003 aluminum core is clad with 4343 aluminum alloy on both sides. This unique construction enhances the tube’s brazing performance, ensuring strong, reliable joints during high-temperature assembly processes. Additionally, the 4343 cladding significantly improves corrosion resistance, protecting the inner core from harsh operating environments, such as those found in automotive, HVAC, and industrial applications.
Compared to the two-layer 4343/3003 variant, the three-layer 4343/3003/4343 design offers superior thermal conductivity and enhanced durability, making it ideal for systems that demand long-term performance and resistance to thermal stress. The combination of high-strength 3003 aluminum and the protective 4343 layers ensures excellent heat transfer efficiency, contributing to overall system performance and energy efficiency. As a result, these tubes play a crucial role in maintaining optimal thermal management across various industries, from automotive cooling systems to industrial heat exchangers.
Structure of 4343/3003 vs 4343/3003/4343 Aluminum High-Frequency Induction Welding Tube
Alloy Type | Structure | Layering | Common Use |
4343/3003 Aluminum High-Frequency Induction Welding Tube | Bimetallic Tube | 2-layer (Clad) | Automotive and industrial radiators |
4343/3003/4343 Aluminum High-Frequency Induction Welding Tube | Sandwich Tube | 3-layer (Double-clad) | More corrosion-resistant heat exchangers |
Composition of 4343/3003 vs 4343/3003/4343 Aluminum High-Frequency Induction Welding Tube
Element | 4343 (Cladding Layer 6%-15% ) wt.% | 3003 (Core Material) wt.% |
Si | 6.8 – 8.2 | ≤ 0.6 |
Fe | ≤ 0.8 | ≤ 0.7 |
Cu | ≤ 0.3 | 0.05 – 0.20 |
Mn | ≤ 0.10 | 1.0 – 1.5 |
Mg | — | ≤ 0.3 |
Zn | ≤ 0.2 | ≤ 0.1 |
Ti | ≤ 0.15 | ≤ 0.1 |
Al | Balance | Balance |
Size of Aluminum High-Frequency Induction Welding Tube
Welded Tube OD (mm) | 16 | 18 | 20 | 22 | 25 | 30 | 31.6 | 31.8 | 32 | 36.5 | 38 | 40 | 43.5 | 50 | 61 |
Drawn Tube OD (mm) | 8 | 9.52 | 10 | 11 | 12 | 13 | 14 | 15 | 18 | 19 | 21 | 23 | 24 | 27 | 28 |
35 | 45 | 54 | |||||||||||||
Wall Thickness (mm) | 0.6 - 3.0mm |
Tolerance of Aluminum High-Frequency Induction Welding Tube
Outer Diameter(mm) | ≤20 | 20-40 | ≥40 |
Outer Diameter Tolerance (mm) | ±0.08 | ±0.1 | ±0.15 |
Wall Thickness (mm) | ≤2.5 | 2.5-3.0 | |
Wall Thickness Tolerance (mm) | ±0.05 | ±0.08 |
Condenser Material (Manifold Tube)
Composite Types: Single-layer & Double-layer
Cladding Layers:
· Materials: 4045, 4343, 7072 (Anti-corrosion layer)
· Optional: Zinc coating for enhanced corrosion resistance
Temper: H14
Cladding Ratio: 10 ± 2%
Core Layer:
· Materials: 3003, 3305
Outer Diameter: 9mm – 61mm
Wall Thickness: 1mm – 3.0mm
Manufacturing Process: High-Frequency Welding
What is High-frequency induction welding?
High-frequency induction welding is a process that uses electromagnetic induction to join materials with precision and efficiency. During this process, an induction coil generates a high-frequency current that surrounds the aluminum tube, creating an induced current within the material. Due to the skin effect and proximity effect, this current concentrates along the edges of the aluminum strip, rapidly heating them to the welding temperature. Under the pressure of extrusion rollers, the heated edges fuse, forming a strong, continuous weld seam. This technique ensures high-precision welding with consistent quality, making it ideal for producing aluminum tubes used in heat exchangers, automotive radiators, and industrial piping. The process enhances the tube’s mechanical strength, corrosion resistance, and thermal conductivity, while its efficiency makes it especially suitable for large-scale manufacturing in industries such as automotive cooling systems, HVAC, construction machinery, and aerospace. High-frequency induction welding not only delivers reliable joints but also supports the production of lightweight, durable components essential for modern engineering applications.